When the question arises whether you should Torque or Tension, the answer is case-sensitive.
Both have the same objective; to create a clamping force that holds parts together. Tensioning is a better system, but not always practical, or necessary.
As Bill Washington, director of business development at FASTORQ said in an interview to Wind Systems magazine, “You want to analyse your bolted joints to determine when you need torque or tension.” “I can tell you that on many flanges, they are over-designed, and torque is fine in many cases. However, you have to use tensioners to get the bolt load you need on critical flanges.”

TORQUE
What is Torquing?
The objective of Torquing is to stretch the bolt or stud to a predetermined load. This is accomplished by turning the nut, which pulls the shank due to the ramp angle of the threads.
Torquing causes the nut to rotate against the surface of the component which is being clamped meaning as the clamp load increases, the friction between the nut and the surface of the component increases to a predetermined amount. This method is less accurate than Tensioning.
Advantages of Torquing
- Less expensive to purchase than Tensioning equipment
- More versatile
- Usually used on smaller fasteners
- Simple to use
The “K Factor”
Torque can do well on most jobs, but you need to consider factors that can hinder getting the proper bolt load from applied torque, such as the “K Factor,” or “nut factor.” The “K Factor” has several components all of which affect preload. These factors are:
- Rust
- Lubricant
- Contaminants
- Washers
- Bolt fit
- Surface conditions,
The Problem with “K Factor” - You can try predict the “K Factor” based on experience, but it is an experimental factor which means you can’t get ‘K’ unless you’ve already tightened the bolt and measured the bolt load. This means you know what “K” was, not what it will be, but if you don’t consider it at all you are certainly going to be wrong.
Dealing with “K Factor” - Although these machines can be costly and require extensive training, one way to deal with “K Factor” issues is to measure bold preload with an ultrasonic extensometer. A less pricey and easier option is use a Load-Indicating Washer, also known as a Direction Tension Indicator (DTI). According to Washington, people can be trained to use DTI’s within 30 seconds.
When Torque is Necessary
Although there are conditions that can affect bolt load when using torque, there are situations where torque is necessary, such as when stud tensioners cannot fit into a space. If torque is necessary, Washington recommends finding a strong and fast torque wrench as only one nut can be tightened at a time.
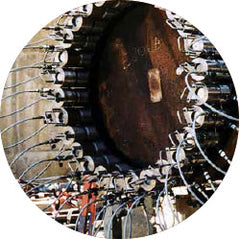
TENSION
What is Tensioning?
Tensioning involves stretching the bolt or stud to a predetermined load by using force to elongate the shank. This is accomplished by a pulling or pushing force created by a hydraulic cylinder. The nut can then be seated manually using a wrench. It is necessary to have some extra thread above the nut, which is used to attach the pulling cylinder, which is removed after completion.
Why Tension?
If you have a problem flange and it is critical that your bolt load is evenly distributed, tensioning is the best solution. While tensioning systems can cost up to 30 times as much as torque wrenches, tensioning is the quickest, most dependable way to attain an even bolt preload when several bolts have to be tightened on a flange.
Advantages of Tensioning
- Can cut down on or even eliminate elastic interactions and over-compression of gaskets.
- Can get rid of many of the obstacles torque faces when reaching desired preload.
- Stability and ease of control
- Highly accurate
- Very little turning force is required.
Disadvantages of Tensioning
Downsides to stud tensioners include:
- Higher load on the first pass that can lead to over compression of gasket material.
- They require more bolt length.
- Can be expensive.
- Often only fit one size bolt.
- More expensive than other systems
What details you need to know to select a Tensioner
Tensioners must be selected specific to each application. Data that must be compiled and considered in the selection of a tensioner include:
- Bolt diameter
- Free stud protrusion length
- Nut size
- Washer thickness and diameter
- Bolt grade
- Bolt load requirement
WHAT IS BEST FOR MY APPLICATION?
Deciding whether you need torque or tension is a question of understanding your needs.
- If you need to tighten several bolts, you can use a high-end torque wrench with load-indicating washers.
- With a critical joint where you want the most precise results and an even bolt load, it’s worth spending investing in tension.
Note: If you have a problem flange and you make your decision strictly based on budget without considering performance, you’ll blow the budget trying to fix it.